
An elastomeric tube with thin and uniform walls is used as an outer jacket of braided shafts. These catheters typically have braided shafts. Column strength, flexibility, and buckling are important mechanical properties for sheath catheters used for stent delivery and electrophysiology catheters for intervention of arrhythmia and atrial fibrillation. In addition, microextrusion techniques are being actively studied to produce steerable or smart catheters. Catheter manufacturing techniques have advanced over time, although more precise catheter manufacturing techniques are still required. The measuring device is used to measure the wall thickness and tube diameter during extrusion.Īs the market for minimally invasive surgery has grown, the demand for high-precision and high-performance catheters has increased. The tube is pulled during extrusion and cut to the desired length in the conveyor system. As extrusion continues, the tube is slightly hardened by quenching, and the lumen of the tube is stably retained as it passes through the vacuum tank filled with water. The pressure of the air injected into the lumen. The initial shape of the tube is formed as the polymer passes through the tip and die.
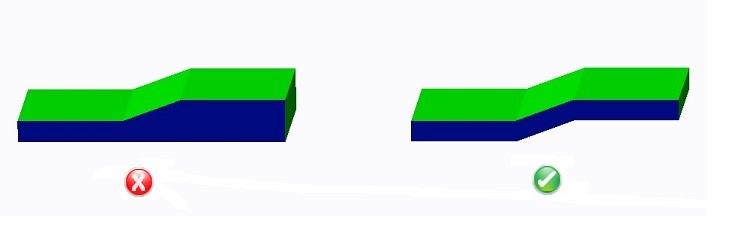
The polymer is dried and dehumidified before being injected through the hopper of the extruder into the screw and barrel, where it melts from the heat of friction among the screw, polymer, and inner wall of the barrel. Extrusion systems have many components, including a dryer and dehumidifier, hopper, screw and barrel, tip and die, quenching system, vacuum water tank, measurement device, puller, cutter, and conveyor system. Therefore, extrusion systems are required that can produce tubes with smaller diameters than those typically manufactured in other industries. In the medical device industry, the outer diameter of the catheter shaft is typically less than 3 mm, while the interventional catheters used in cardiovascular and cerebrovascular fields have outer diameters of 1 mm or less. Today, catheters are commonly fabricated from thermoplastic elastomers through an extrusion process. During use, the distal portion of the catheter (the far end) is steered unidirectionally or bidirectionally. These thin tubes are generally 300–2000 mm long, with a single-lumen (cavity in the tube) or multi-lumen cross-section and a braided or coiled shaft to meet the demands of the application.
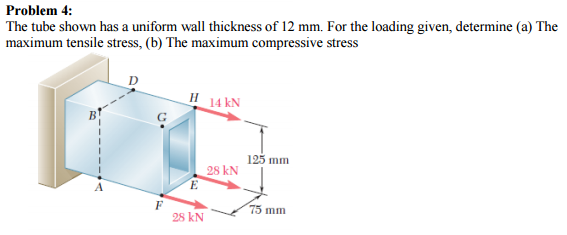
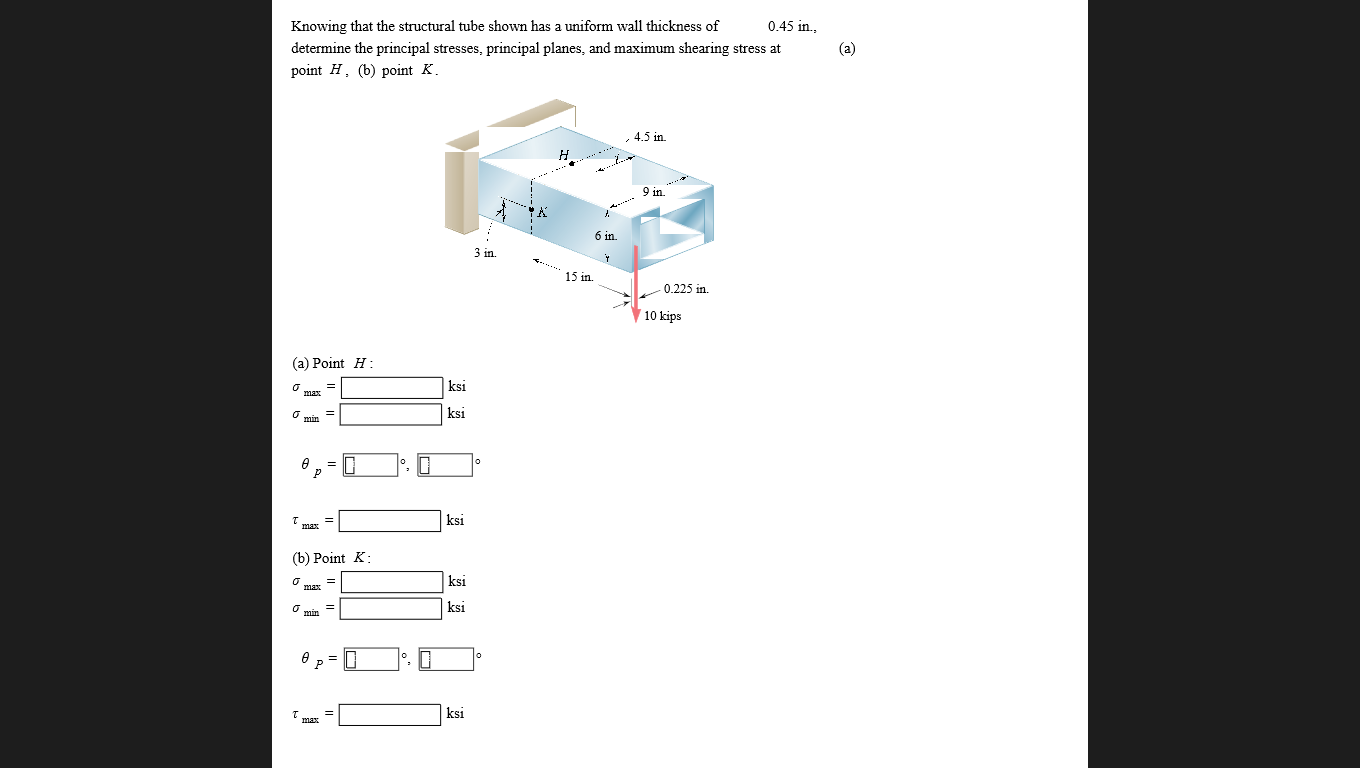
The results show the effect of different processing parameters on the characteristics of the extruded tube, which will help to establish a stable extrusion process for the manufacture of outer jackets for braided catheter shafts.Ĭatheters are minimally invasive interventional medical devices actively used in numerous procedures, including stent delivery, drug and contrast injection, imaging guide diagnosis, and ablation. The air pressure and distance between quench and head had the greatest influence on ovality. The screw speed (mass flow rate), puller speed, and air pressure affected the inner/outer diameter of the tube, with screw speed and puller speed having the largest influence on diameter. The ovality and inner/outer diameters of the tube were studied according to changes in the screw speed (mass flow rate), puller speed, air pressure applied to the lumen, and distance between the quench and head, which are the main variables of microextrusion processes. In this study, we designed and manufactured a tip and die capable of extruding an outer jacket with a wall thickness of 150 µm or less using a medical thermoplastic elastomer for manufacturing 8Fr (2.64 mm diameter) thin-walled tubes. The outer jacket should have an accurate inner and outer diameter and while maintaining a wall thickness of 150 µm or less. Catheters for the diagnosis and treatment of cardiovascular or cerebrovascular disease mainly use a braided wire tube with a polymer inner liner and outer jacket to improve the pushability and trackability. As the market for minimally invasive surgery has grown, the demand for high-precision and high-performance catheters has increased.
